Jednym z kluczowych problemów, z którymi mierzą się użytkownicy pomp membranowych, są awarie wynikające z szybkiego zużycia membran. Przyczyniają się one do przestojów, obniżenia efektywności systemów oraz zwiększenia kosztów eksploatacji. Poniżej omówimy główne powody tego zjawiska oraz przedstawimy sprawdzone metody na wydłużenie żywotności membran i zapobieganie awariom.
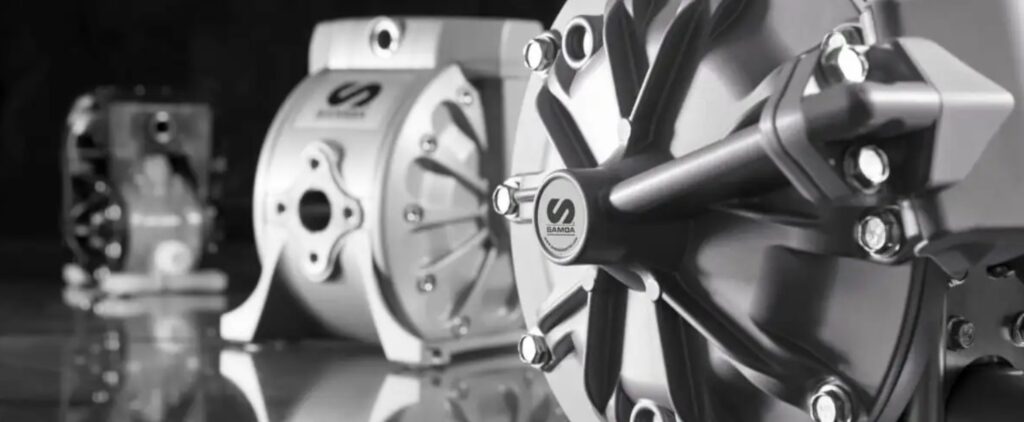
Problemy z pracą pomp membranowych na sucho – jak im zapobiegać?
Kiedy pompa membranowa pracuje na sucho, bez przepływającego płynu, działa znacznie szybciej niż podczas standardowego transferu medium. W takich warunkach nie tylko wzrasta zużycie sprężonego powietrza, co generuje straty energii, ale również dochodzi do przyspieszonego zużycia membran. Oto dwa główne wyzwania wynikające z pracy na sucho:
1. Straty energetyczne – drastyczny wzrost zużycia sprężonego powietrza powoduje niepotrzebne marnotrawstwo energii, co zwiększa koszty eksploatacji.
2. Koszty konserwacji – praca na sucho przyspiesza zużycie membran, skracając ich żywotność i prowadząc do częstszych przestojów w celu wymiany części.
Praca na sucho jest jedną z najczęstszych przyczyn przedwczesnych uszkodzeń pomp z podwójną membraną. Aby temu zapobiec, warto zastosować następujące rozwiązania:
- Zabezpieczenia przed pracą na sucho – stosowanie urządzeń kontrolujących przepływ płynu eliminuje ryzyko pracy pompy bez medium.
- Monitorowanie prędkości pompy – wykorzystanie czujników zewnętrznych pozwala kontrolować prędkość pracy i uniknąć nadmiernego obciążenia.
Dodatkowo warto zwrócić uwagę na zjawisko kawitacji, które występuje, gdy przepływ na ssaniu jest ograniczony. Kawitacja prowadzi do podobnych skutków, takich jak nadmierne zużycie membran i skrócenie ich żywotności. Regularne monitorowanie warunków pracy pompy oraz stosowanie odpowiednich zabezpieczeń pozwala zminimalizować ryzyko tych problemów i zapewnić niezawodność systemu.
Odporność fizykochemiczna
Odporność materiałów na substancje chemiczne w pompach membranowych
W pompach membranowych elementy mające kontakt z cieczą, takie jak membrany, kulki czy gniazda, muszą wykazywać wysoką odporność na działanie substancji chemicznych. Przedwczesne uszkodzenia membran, objawiające się pękaniem, odbarwieniami lub efektem bulgotania, mogą świadczyć o nieodpowiednim dobraniu materiałów do medium, co prowadzi do tzw. ataku chemicznego.
Jak zapobiegać uszkodzeniom?
- Analiza aplikacji – dokładne poznanie właściwości chemicznych przenoszonej substancji.
- Dobór odpowiednich materiałów – wybór elementów o potwierdzonej kompatybilności chemicznej, co pozwala uniknąć degradacji materiałów w kontakcie z cieczą.
- Przewodnik kompatybilności – skorzystanie z tabeli odporności chemicznej udostępnianej przez producenta pompy membranowej.
W razie wątpliwości zawsze warto skonsultować się z producentem lub ekspertem technicznym, aby mieć pewność, że wybrane materiały spełniają wymagania aplikacji. Dzięki temu można uniknąć awarii i zapewnić długą żywotność pompy.
Proces tłoczenia: Jak uniknąć uszkodzeń membran w pompach?
Podczas uruchamiania pompy membranowej i zasysania medium po raz pierwszy należy stopniowo zwiększać ciśnienie powietrza, pamiętając o pozostawieniu otwartego zaworu wylotowego. Pompa zacznie efektywnie zasysać ciecz, gdy przepływ przez zawór wylotowy stanie się równomierny.
Zagrożenia związane z ciśnieniem
Ciśnienie powietrza wywierające nacisk na membranę może prowadzić do jej nadmiernego odkształcenia. W przypadku przekroczenia zalecanego limitu ciśnienia, membrana może ulec trwałym uszkodzeniom. Aby temu zapobiec, maksymalne ciśnienie powietrza nie powinno przekraczać 8 barów.
Jak uniknąć uszkodzeń membran?
- Stosowanie regulatorów ciśnienia – specjalne regulatory pomagają kontrolować ciśnienie wlotowe powietrza, zapobiegając jego nadmiarowi.
- Optymalizacja prędkości pompy – reduktor ciśnieniowy pozwala dostosować prędkość pracy pompy do wymagań aplikacji, co zwiększa żywotność membran.
Zapewnienie odpowiedniego ciśnienia roboczego i zastosowanie regulatorów powietrza pozwala uniknąć kosztownych awarii oraz wydłużyć czas eksploatacji pompy membranowej.
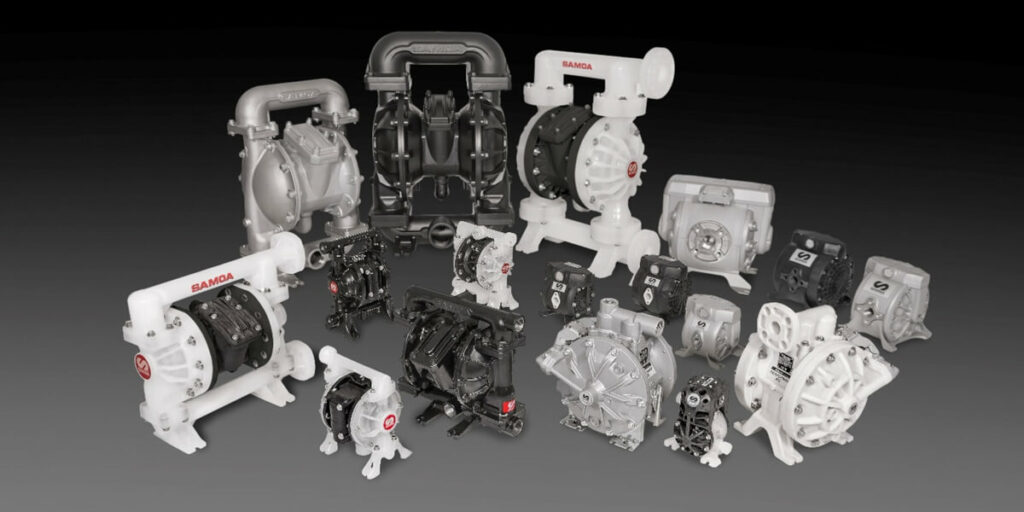
Ważne zasady eksploatacji pomp membranowych
Aby zapewnić niezawodność i długą żywotność pomp membranowych, należy zwrócić szczególną uwagę na dwa kluczowe czynniki: ciśnienie wlotowe płynu oraz ciśnienie powietrza. Oto, jak unikać problemów:
1. Nadmierne ciśnienie wlotowe płynu
Jeśli ciśnienie wlotowe płynu przekracza 10 psi (0,69 bara), może dojść do poważnych uszkodzeń, takich jak:
- Implozja membran – powoduje ich trwałe uszkodzenia.
- Ocieranie się membran o komorę powietrzną – dodatkowo pogarsza problem, skracając żywotność pompy.
Ten problem często pojawia się w aplikacjach, gdzie pompa jest zasilana z wysokiego zbiornika lub pracuje z cieczą o dużej gęstości. Aby temu zapobiec:
- Zainstaluj zawór redukcyjny na wlocie płynu do pompy.
- Zmniejsz poziom płynu w zbiorniku, aby ograniczyć nadmierne ciśnienie hydrostatyczne.
2. Nadmierne ciśnienie powietrza wlotowego
Zbyt wysokie ciśnienie powietrza może prowadzić do awarii membran, takich jak pęknięcia lub rozszczelnienia. Maksymalne dopuszczalne ciśnienie wlotowe wynosi:
- 8 bar (120 psi) dla pomp metalowych.
- 7 bar (100 psi) dla pomp niemetalowych.
Aby uniknąć problemów:
- Zastosuj regulator ciśnienia powietrza przed pompą, aby kontrolować dopływ powietrza.
- Monitoruj warunki pracy, aby utrzymać ciśnienie w bezpiecznym zakresie.
Przestrzeganie tych zasad minimalizuje ryzyko uszkodzeń, zwiększa niezawodność systemu i redukuje koszty związane z wymianą membran oraz przestojami produkcyjnymi.
Prawidłowe dokręcanie śrub w pompie membranowej
W szczególności dla pomp wykonanych z tworzyw sztucznych, zaleca się dokładne dokręcenie wszystkich śrub przed pierwszym uruchomieniem. W trakcie transportu elementy mocujące mogą ulec poluzowaniu, co może wpłynąć na wydajność i trwałość pompy. Należy ściśle stosować się do specyfikacji momentu obrotowego podanych w dokumentacji technicznej producenta.
Dlaczego jest to istotne?
- Zbyt mocne dokręcenie – jeśli membrany zostaną dokręcone z nadmiernym momentem, ich krawędzie mogą ulec uszkodzeniu, co może prowadzić do powstawania nacięć i skrócenia ich żywotności.
- Zbyt słabe dokręcenie – w przypadku niedostatecznego momentu dokręcenia membrany mogą zostać przeciągnięte, co zwiększa ryzyko wycieków lub uszkodzeń w trakcie pracy.
Jak uniknąć problemów?
- Sprawdź i zastosuj momenty dokręcenia zgodnie z instrukcją obsługi.
- Regularnie kontroluj stan śrub mocujących podczas eksploatacji pompy, szczególnie po transporcie lub dłuższych przestojach.
Prawidłowe dokręcenie pompy gwarantuje jej bezawaryjną pracę, chroni membrany przed uszkodzeniami oraz wydłuża żywotność urządzenia.
Jak ograniczyć zużycie pomp podczas pracy z płynami ściernymi?
Pompowanie cieczy o właściwościach ściernych, takich jak atramenty czy zawiesiny, może prowadzić do szybkiego zużycia elementów pompy. Aby zminimalizować skutki ścierania, warto zwrócić uwagę na dwa kluczowe czynniki:
- Rozmiar pompy – większe pompy są bardziej odporne na zużycie i lepiej radzą sobie z przenoszeniem ściernych cieczy.
- Prędkość pracy – wolniejsza praca pompy pozwala na zmniejszenie ścierania i wydłuża żywotność jej komponentów.
Dobre praktyki w przypadku płynów ściernych:
Przewymiarowanie pompy oraz ustawienie jej na wolniejszą pracę to skuteczny sposób na redukcję ścierania. Ciągłe pompowanie ściernych cieczy może powodować zużycie szczególnie w obszarach między membraną a zewnętrznym tłokiem cieczy.
Jak zmniejszyć wpływ ścierania?
- Zredukowanie prędkości pompy – można to osiągnąć poprzez zastosowanie regulatora ciśnienia powietrza i zmniejszenie ciśnienia zasilającego.
- Wybór odpowiedniego rozmiaru – jeśli wymagane jest wysokie ciśnienie tłoczenia, a zmniejszenie ciśnienia powietrza nie jest możliwe, zastosowanie większej pompy pozwoli zmniejszyć prędkość roboczą, co ograniczy zużycie.
Dostosowanie parametrów pracy pompy i wybór właściwego modelu pozwalają na znaczne zmniejszenie ścierania i zwiększenie trwałości urządzenia przy pracy z wymagającymi mediami.
Zanieczyszczenia w pompach membranowych: jak zapobiegać uszkodzeniom?
Pompy przemysłowe membranowe są przystosowane do przenoszenia cieczy zawierających drobne cząstki stałe w zawiesinie. Jednak w przypadku cieczy o wysokim stężeniu ciał stałych, zaleca się zastosowanie odpowiednich filtrów. Filtry pełnią kluczową rolę w ochronie pompy, zapobiegając przedostawaniu się zanieczyszczeń do jej wnętrza.
Dlaczego filtry są ważne?
- Ochrona membran – filtry minimalizują ryzyko uszkodzeń membran spowodowanych obecnością większych cząstek stałych.
- Wydłużenie żywotności pompy – redukcja zanieczyszczeń zmniejsza ścieranie i przeciążenie kluczowych elementów pompy.
Jak działać prewencyjnie?
- Dobierz filtr do aplikacji – wybierz filtr odpowiedni do rodzaju cieczy i wielkości cząstek stałych.
- Regularna konserwacja – czyszczenie lub wymiana filtrów w odpowiednich odstępach czasu zapewni optymalną pracę pompy.
- Monitorowanie pracy – Systematyczna kontrola układu pozwoli wychwycić ewentualne problemy, zanim wpłyną one na działanie pompy.
Stosowanie filtrów to prosta, ale skuteczna metoda ochrony pomp membranowych przed uszkodzeniami spowodowanymi przez zanieczyszczenia, co przekłada się na ich większą niezawodność i wydłużoną żywotność.
Odpowiedni zakres temperatur pracy pomp membranowych
Aby uniknąć takich problemów jak odbarwienia, pęknięcia, bulgotanie czy inne uszkodzenia, kluczowe jest dostosowanie temperatury roboczej do materiałów, z których wykonana jest pompa. Każdy materiał ma określony zakres temperatur, w którym działa optymalnie:
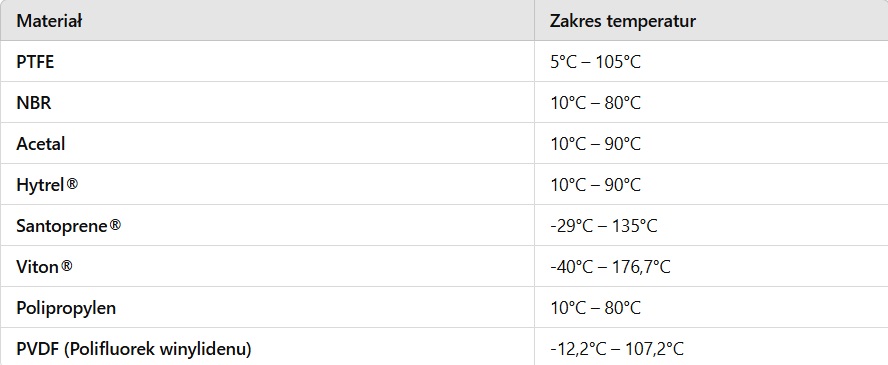
Dlaczego warto przestrzegać zakresów temperatur?
- Zapobieganie uszkodzeniom – praca poza zalecanym zakresem może prowadzić do mechanicznych uszkodzeń lub deformacji materiałów.
- Optymalna wydajność – przestrzeganie zakresów temperatur gwarantuje niezawodne działanie pompy.
- Dłuższa żywotność – unikanie ekstremalnych warunków pozwala zminimalizować zużycie i konserwację.
Dostosowanie pompy do specyficznych warunków temperaturowych aplikacji pozwoli uniknąć awarii i utrzymać wysoką efektywność pracy systemu. W przypadku wątpliwości warto skonsultować się z producentem w celu wyboru najlepszego rozwiązania dla danej aplikacji.
Problemy wynikające z niewłaściwego zakresu temperatur pracy
Aby uniknąć przedwczesnych uszkodzeń pompy membranowej oraz awarii membran, kluczowe jest przestrzeganie odpowiednich zakresów temperatur roboczych, dostosowanych do materiałów, z których wykonano pompę. Praca w niewłaściwym zakresie temperatur może prowadzić do szeregu problemów, takich jak:
- Przebarwienia membran – powstają w wyniku długotrwałego działania wysokich temperatur.
- Pęknięcia i deformacje – ekstremalne temperatury mogą osłabić strukturę membrany, prowadząc do pęknięć lub efektu bulgotania.
Jak uniknąć uszkodzeń?
- Wybierz pompę odporną na temperatury aplikacji – w przypadku pracy z cieczami o wysokiej temperaturze zaleca się wymianę pompy na model wykonany z bardziej odpornych materiałów.
- Stosuj zestawy naprawcze – jeśli problem dotyczy jedynie membran, ich wymiana na odpowiednie, dostosowane do wymaganej temperatury, może skutecznie rozwiązać problem.
- Regularna konserwacja – systematyczne przeglądy pozwalają wcześnie zidentyfikować oznaki uszkodzeń i zapobiec poważnym awariom.
Przestrzeganie zaleceń producenta oraz dobór odpowiednich materiałów zapewnią dłuższą żywotność pompy i niezawodność w nawet najbardziej wymagających aplikacjach.
Wytrzymałe membrany SAMOA – jakość na pierwszym miejscu
Firma SAMOA dostarcza membrany wykonane z najwyższej jakości materiałów, co przekłada się na ich wyjątkową trwałość i dłuższą żywotność. Membrany PTFE są specjalnie zaprojektowane jako jednoczęściowe, zbudowane z trzech zintegrowanych warstw:
- Warstwa EPDM – znajdująca się od strony powietrza, zapewnia doskonałą odporność na zmienne ciśnienia.
- Warstwa centralna – wykonana z tekstyliów, wzmacnia strukturę membrany, zwiększając jej wytrzymałość.
- Warstwa PTFE – po stronie płynu, chroni przed agresywnymi chemikaliami i ścieraniem.
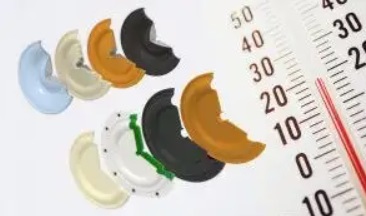
Taka konstrukcja nie tylko zwiększa odporność membran na uszkodzenia, ale także znacznie wydłuża ich żywotność, co czyni je idealnym wyborem do wymagających zastosowań przemysłowych. SAMOA gwarantuje niezawodność i najwyższą jakość swoich produktów, dostosowaną do potrzeb najbardziej wymagających aplikacji.
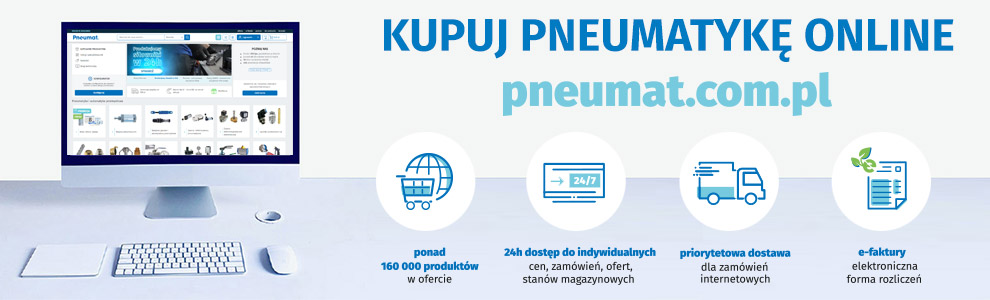
Dodaj komentarz